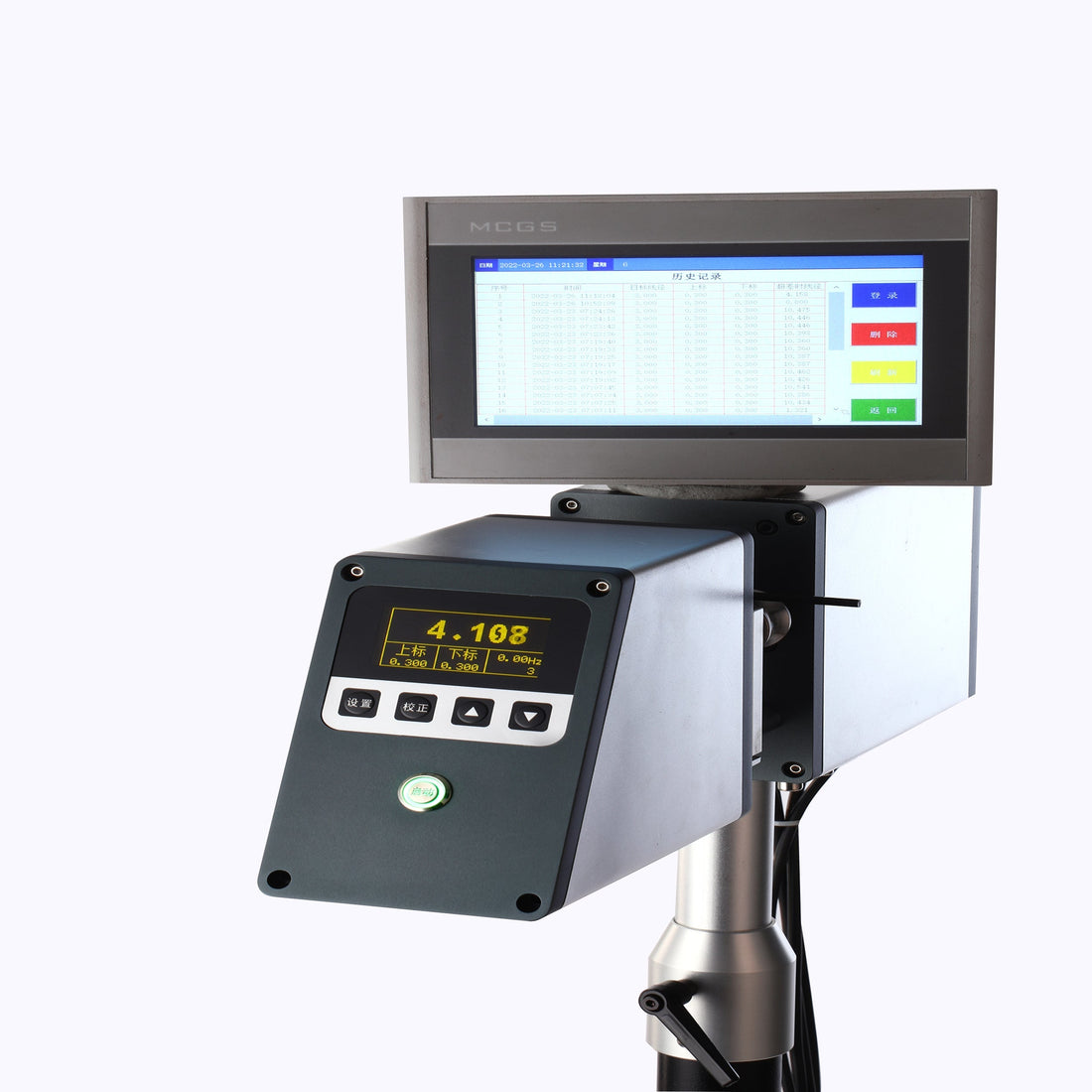
Laser Diameter Gauge: Application Scenarios and Advantages Analysis
Kongsi
Laser Diameter Gauge: Application Scenarios and Advantages Analysis
In modern industrial production and scientific research, precise measurement of object dimensions is a critical step in ensuring product quality and performance. As a non-contact, high-precision measurement tool, the laser diameter gauge, with its unique technical advantages, is gradually replacing traditional diameter measurement methods and becoming an indispensable device in many industries. This article will explore the application scenarios of laser diameter gauges in detail and analyze their advantages compared to traditional measurement methods.
I. Application Scenarios of Laser Diameter Gauges
Laser diameter gauges have a wide range of applications, covering almost all fields that require high-precision measurement of object dimensions. Below are some typical application scenarios:
1. Wire and Cable Industry
· Application Scenario: During the production of wires and cables, it is necessary to monitor the outer diameter and insulation thickness in real time to ensure products meet standards.
· Role of Laser Diameter Gauge: Through non-contact measurement, the laser diameter gauge can quickly and accurately measure the outer diameter and insulation thickness of cables, avoiding potential damage to the insulation layer caused by traditional contact measurements.
2. Optical Fiber Communication Industry
· Application Scenario: The diameter and concentricity of optical fibers are key parameters affecting their transmission performance and must be strictly monitored during production.
· Role of Laser Diameter Gauge: The laser diameter gauge can measure the diameter and concentricity of optical fibers with micrometer-level precision, ensuring high-quality production.
3. Bearing Manufacturing Industry
· Application Scenario: The dimensional accuracy of bearing inner and outer diameters and ball diameters directly affects their service life and performance.
· Role of Laser Diameter Gauge: The laser diameter gauge can quickly measure multiple critical dimensions of bearings, ensuring products meet design requirements.
4. Pipe and Rod Industry
· Application Scenario: In the production of metal or plastic pipes and rods, real-time monitoring of outer diameter and wall thickness is required.
· Role of Laser Diameter Gauge: The laser diameter gauge can perform online measurements on production lines, providing real-time feedback to help adjust production processes.
5. Glass Manufacturing Industry
· Application Scenario: The thickness and flatness of glass are important indicators of its quality.
· Role of Laser Diameter Gauge: The laser diameter gauge can measure the thickness and flatness of glass without contact, avoiding scratches caused by traditional measurement methods.
6. 3D Printing and Precision Manufacturing
· Application Scenario: In 3D printing and precision manufacturing, high-precision measurement of tiny components is required.
· Role of Laser Diameter Gauge: The high precision and non-contact nature of the laser diameter gauge make it an ideal tool for measuring small parts.
II. Comparison Between Laser Diameter Gauges and Traditional Measurement Methods
Compared to traditional measurement methods (such as micrometers and calipers), laser diameter gauges demonstrate significant advantages in several aspects:
1. Non-Contact Measurement
Traditional Methods: Tools like micrometers and calipers require direct contact with the measured object, which may cause surface scratches or deformation.
Laser Diameter Gauge: No contact with the object is needed, making it particularly suitable for measuring soft, fragile, or high-temperature objects.
2. High Precision
Traditional Methods: The measurement accuracy of traditional tools is typically around 0.01 mm, which struggles to meet high-precision requirements.
Laser Diameter Gauge: Measurement accuracy can reach the micrometer level or even higher, suitable for high-precision manufacturing and scientific research.
3. Fast Measurement
Traditional Methods: Manual measurement is slow and difficult to achieve real-time monitoring.
Laser Diameter Gauge: Measurement speed is extremely fast, enabling real-time online measurement and significantly improving production efficiency.
4. Automation and Intelligence
Traditional Methods: Reliance on manual operation can introduce human errors.
Laser Diameter Gauge: Can be connected to computers or control systems for automated measurement and data recording, reducing human errors.
5. Multifunctionality
Traditional Methods: Typically limited to measuring a single parameter (e.g., diameter or thickness).
Laser Diameter Gauge: Can measure multiple parameters simultaneously (e.g., diameter, thickness, ellipticity) and supports scanning measurements to obtain cross-sectional shapes of objects.
6. Adaptability to Harsh Environments
Traditional Methods: Difficult to use in high-temperature, high-pressure, or corrosive environments.
Laser Diameter Gauge: Can operate stably in harsh environments with strong adaptability.
III. Future Development Trends of Laser Diameter Gauges
With the advancement of Industry 4.0 and smart manufacturing, laser diameter gauges are moving toward higher precision, faster speeds, and greater intelligence. For example:
Integration of AI Technology: Optimizing measurement results through artificial intelligence algorithms to improve accuracy.
Multi-Dimensional Measurement: Expanding from single-dimension measurement to three-dimensional shape measurement.
Cloud Data Management: Uploading measurement data to the cloud for remote monitoring and analysis.
IV. Conclusion
With its advantages of non-contact measurement, high precision, and fast measurement, the laser diameter gauge is gradually replacing traditional measurement methods and becoming an essential tool in modern industrial production and scientific research. Whether in the wire and cable industry, optical fiber communication, precision manufacturing, or 3D printing, laser diameter gauges have demonstrated significant application potential. As technology continues to advance, laser diameter gauges will play an even greater role in more fields, providing more accurate and efficient measurement solutions for industrial production and scientific research.